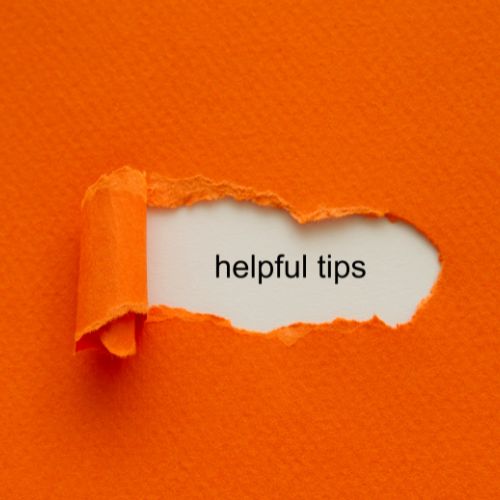
Below you can find 5 tips that will help you to reduce asset downtime from today.
Know What Assets You Have
When you use a reliable asset register format you can see exactly what you have. So, if something does break down you know how many replacements you have. You’ll also know whether you’ll have the right tools to fix that broken down conveyor belt.
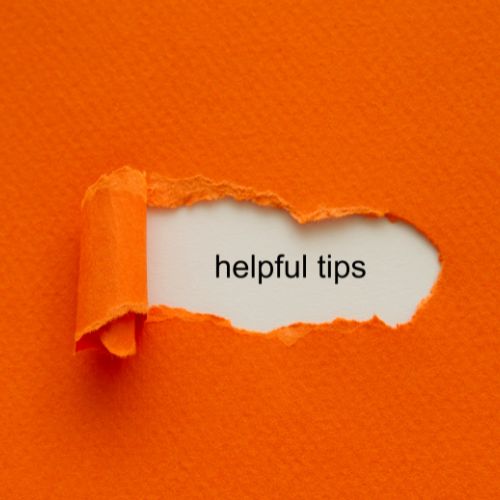
Use Asset Tracking Software
Did you know that a digital asset register format could allow you to leave notes about equipment? If you used a hammer drill, for example, and it wasn’t working well, you could leave a note for the next person. You could tell them to make sure the drill bit is in properly. You could mention that the drill needs to be fully charged before use. You could tell them whatever you wish using the asset tracking software. So, the next time that hammer drill is used, someone will know exactly what to do.
Set Up A Maintenance Schedule
You could, for example, set up a schedule for each asset at intervals that are ideal for them. For example, that hammer drill could be scheduled for maintenance every six months. A vehicle could be checked out once a year. Your conveyor belt and the rest of the production equipment could be examined every 3 months. The choice is ultimately yours. However, when you do set up a maintenance schedule you could find that downtime is minimal. All of your tools, equipment, and vehicles, etc. will be taken care of. Issues and faults are more likely to be found and dealt with. Consequently, downtime could be reduced and productivity can increase.
Use Pre-emptive Maintenance
Check Everything In And Out
The last and one of the least considered options for reducing downtime revolves around checking assets in and out. When you check equipment in and out you can see which ones are about to go for maintenance. If that hammer drill has died, you may be able to see that it’s on its way to be repaired. As a result, you could look for another drill to use instead.
When you check everything in and out you can also see who’s using which assets. You’ll learn whether you have to wait for the asset and even if there’s an issue with them. This feature saves downtime by showing you which assets can and can’t be used. You can also see which assets are being repaired and whether they’re likely to come back any time soon. As a result, downtime can be reduced and you can get on with the task at hand.
Wish to speak with someone knowledgeable about a new asset register format that reduces downtime? Contact us now at team@itemit.com
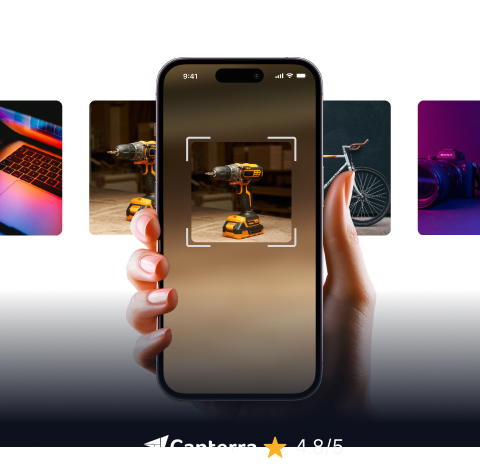
Try itemit
Choose a better way to track your assets. Start your free 14-day trial now!
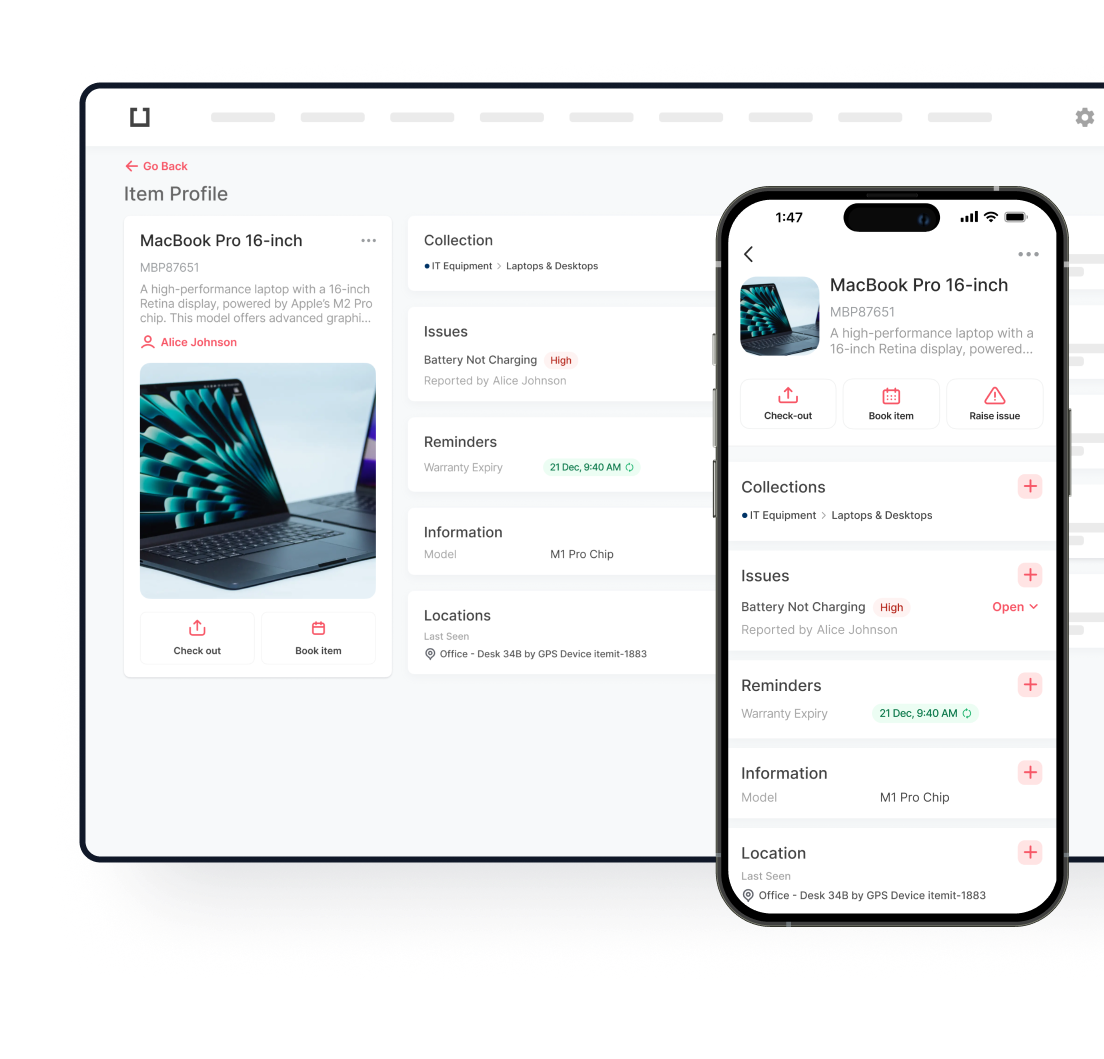
Keep Learning
itemit Blog
Tips, guides, industry best practices, and news.
How to Track Assets Using GPS trackers
GPS trackers have become an increasingly popular way for businesses to track their assets. Discover exactly how to use GPS trackers to track your assets.
What Is Cloud-Based Software?
What does it really mean to store something in the cloud or to have cloud-based software? Read on to discover what it’s all about.
Everything You Need to Know on Tracking IT Assets
The right IT asset tracking software can help businesses of all shapes and sizes to function on a daily basis. Find out more here!