When equipment breaks down or is in need of repair it can slow things down immensely. For example, those orders may not be fulfilled by midday. The machine that you work with every day may stop functioning completely, causing tailbacks, etc.
Downtime is something that can cause a lot of issues, even if it lasts for just a few minutes. The good news is that there are a few strategies for reducing equipment downtime. This is where pre-emptive maintenance can come in and make a real difference. Let’s explore this and other strategies now.
Use a Computerised Maintenance Management System
A computerised maintenance management system (CMMS) can help to reduce human errors that can increase downtime. A CMMS that is worth its weight in gold can potentially help by tracking maintenance. Additionally, it can ensure that the maintenance team has easy access to instruction manuals. As a result, repairs can be made as and when they are required.
Equipment maintenance planning that comes as standard with many CMMSs can have maintenance procedures that are almost foolproof. Such planning can ensure that inspections and repairs take place. Pre-emptive maintenance is a major part of this.
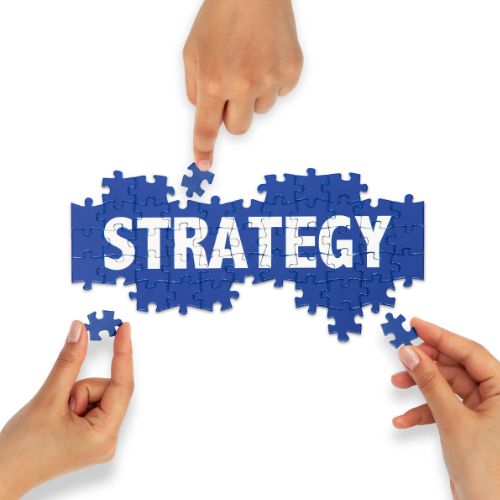
Have A Back-Up Plan
It always makes sense to have a back-up plan. No matter what type of business you have or how large your business is, a back-up plan can help. Equipment can fail at a moment’s notice and at critical times.
We’ve all experienced occasions when we really need all of our machinery to work with no issues. However, it seems that when there’s a right deadline something usually goes wrong. Here is where having a back-up plan can help.
A back-up plan can include having generators kick in when the power’s down. It can include using other machinery to complete tasks when another machine has stopped working.
No matter what your back-up plan may be, if you have one that works, it could save the day. You could, for example, ship those orders on time. You may be able to write that report before the deadline so your manager is happy.
Always have a back-up plan. When you do, you can still work even when your equipment, tools, computer, or machinery decide to stop working at the most crucial moment.
Use Pre-emptive Maintenance To Your Advantage
One of the very best strategies for reducing equipment downtime is by using pre-emptive maintenance. When you use this strategy to its full advantage there’s a real chance that you can make a difference.
Pre-emptive maintenance is all about making sure that you prevent maintenance issues before they arise. While this may seem easier said than done, with the use of some tracking software, it’s entirely possible.
Let’s take a look at just how pre-emptive maintenance can make a real difference.
You Can Notify The Maintenance Team Of Potential Issues
Using software that helps you to track your equipment may also allow you to deal with maintenance issues. For example, if the tablet you’re using does not always respond to your touch, you could notify the maintenance department.
Some tracking software allows you to send messages to different departments. If the software that you use permits this, you could notify the maintenance team of the issue. The team can then repair the tablet before the issue becomes worse. As a result, downtime can be kept to a minimum.
It is likely that you will have more than one tablet available for use at any one time. This means that repairing one of them may not cause major issues. However, if more than one tablet is in need of repair, downtime could become a problem. This is where pre-empting issues can make a real difference.
You Can Set Up A Maintenance Schedule
Setting up a maintenance schedule is, perhaps, one of the best pre-emptive maintenance strategies around. If you want to reduce equipment downtime, this is the strategy to use.
A maintenance schedule can be attuned to every piece of equipment that you have. For example, your largest conveyor belt could be serviced every 6 months. Your grinding and milling machines could be serviced every 3 months. The choice is yours.
One of the best things about setting up a maintenance schedule is its notifications. You can potentially receive notifications just before your equipment needs to undergo maintenance. As a result, it may be possible for you to organise the usage of other equipment in the meantime. Alternatively, you may simply need to have some downtime while the equipment is being maintained. The good news is that if you stick with the schedule, downtime can be minimised. In addition to this, if potential issues are always flagged, downtime can be reduced even further.
Would you like to speak with someone about pre-emptive maintenance? Contact us today. You can reach us now at: team@itemit.com. We’re here to help you.
The Ideal Way To Reduce Equipment Downtime
Choose a better way to track your assets
Start your free 14-day trial now
Instant access. No credit card details required.
You can also start your 14-day free trial by filling out the form below, or you can contact us at team@itemit.com or at 01223 421611.
Or, you can check out these blogs:
What Are the Best Asset Management Tracking Tools?
3 Ways Fixed Asset Tracking Software Saves you Time and Money
How to Track Maintenance with Heavy Equipment Maintenance Software
Latest posts
itemit Blog
Tips, guides, industry best practices, and news.
Latest posts
itemit Blog
Tips, guides, industry best practices, and news.
Related articles
Exploring Different Types of Inventory and Their Impact on Asset Tracking
Learn about the 4 types of inventory—raw materials, WIP, finished goods, and MRO—and their impact on asset tracking. Discover strategies for better inventory management.
Inventory Planning Best Practices: Avoid Stockouts and Overages with Asset Tracking
Discover inventory planning best practices to avoid stockouts and overages. Learn how asset tracking improves accuracy, reduces waste, and optimizes supply chain management.
Markup vs. Margin Difference: Optimise Inventory Profitability
Learn the key differences in margin vs markup in inventory management. Understand how each affects pricing, profitability, and business growth to optimize your strategy