Replacing equipment can seem unduly expensive. Trying to salvage a broken down asset often has good results, however, this is not always possible. Some equipment may be too damaged to repair so it needs to be replaced.
Here is where having an effective equipment replacement plan can help. If you have already used pre-emptive maintenance to its full advantage there may be nothing else you can do. Therefore, it may be time to use your equipment replacement plan to its full advantage.
But what exactly is an equipment replacement plan? Let’s take a look so you can create one and use it to its full advantage.
Pin Down Your Budget
The very first thing you need to do is to pin down your budget. In other words, work out how much you can spend on equipment replacement after pre-emptive maintenance and other methods have failed.
It’s thought that approximately 1.5% to 4.6% of your yearly revenue budget should be spent on replacing your equipment. However, every 7 years or so, you may need to spend as much as 12%-15% on replacing equipment. If you purchased a lot of assets at the same time, they may break down at the same time. Try to prevent big spending by using pre-emptive maintenance so your assets are less likely to break down.
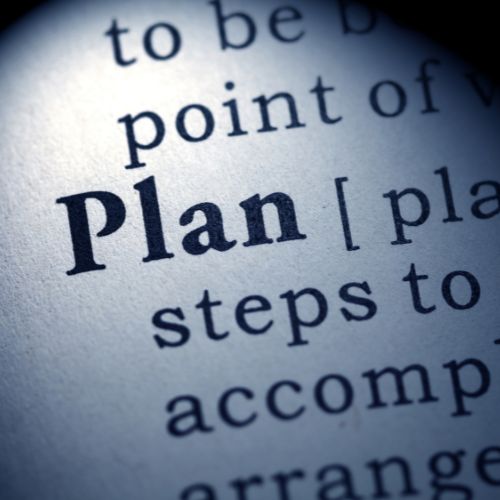
Keep Detailed Financial Records
Keeping detailed records of how much you have spent on your equipment is important. Add information such as the costs of pre-emptive maintenance and replacement parts. When you keep a record of information such as this, you can see what the costs are for each vehicle, computer, machine, and so on. When you know how much a machine, for example, costs, you’ll have a better idea about whether it should be replaced or repaired.
Assess The Need For Equipment Replacement
Once you know how much it will cost to replace broken down machinery, computers, etc. you can assess the need to replace it. Your assets, no matter what they are, can fit into 1 of 3 replacement categories. These categories are:
- 1. Critical
- 2. Moderate
- 3. Low
You could rank all of your assets as soon as everything has been added to a category. When you know how important it is to replace something you know which direction to take with it. For example, if an asset is in the critical ‘box’, you may need to replace it ASAP. If something is in the low ‘box’ you could replace it within the next month or so.
Work Out The Cost Of Replacement
Now you know when you need to replace something it’s time to work out the cost of doing so. Get quotes for the replacement equipment. Do this for equipment in all of the above categories. Your assets can it into 1 of 3 cost categories:
- 1. Low cost
- 2. Moderate cost
- 3. High cost
Determine When To Replace Equipment
As soon as you have assessed the need for equipment replacement and you understand the cost it’s time to work out exactly when to replace it. Take the number of the equipment replacement box, for example, “2. Moderate” and the cost box, for example, “3. High cost”.
Add the numbers together, they should be anywhere from 2 to 6. When you have an asset that scores 2, it means it needs to be replaced quickly and the cost is low. If an asset has a moderate replacement need and a high cost the score will be 5. The lower the score is, the better, of course.
Now you have this information you can compare it to the asset’s life span. This can help you to make your replacement decisions.
Formulate Your Plan
The final step is to formulate your plan. You’ve added the numbers, you’ve completed pre-emptive maintenance and you’ve pinned down your budget. Now it’s time to share it with those who need to see it so they can have a say if needs be. For example, someone may think that it’s more important to replace a computer than it is a vehicle. They may also be able to get a much cheaper quote.
As soon as everyone has had their say, it’s time to work out when to purchase your new machine and have it delivered ASAP. Reducing downtime is a priority here so the sooner your machine is with you, the better.
Once your plan has been formulated and worked out, you can use it the next time something chooses to break down. As we all know, this is likely to be when you have a large order or when you’re extremely busy. In any case, if you have an effective equipment replacement plan to hand, replacing equipment will be much easier. As a result, you can complete important tasks sooner and keep your business running smoothly.
Would you like to speak with an expert about creating an effective equipment replacement plan? Contact us now at: team@itemit.com.
The Best Way To Implement An Effective Equipment Replacement Plan
Choose a better way to track your assets
Start your free 14-day trial now
Instant access. No credit card details required.
You can also start your 14-day free trial by filling out the form below, or you can contact us at team@itemit.com or at 01223 421611.
Or, you can check out these blogs:
What Are the Best Asset Management Tracking Tools?
3 Ways Fixed Asset Tracking Software Saves you Time and Money
How to Track Maintenance with Heavy Equipment Maintenance Software
Latest posts
itemit Blog
Tips, guides, industry best practices, and news.
Latest posts
itemit Blog
Tips, guides, industry best practices, and news.
Related articles
How to Calculate Beginning Inventory: Formula & Examples
Learn how to calculate beginning inventory using simple formulas. Understand its importance in inventory management and financial tracking. Read more!
How to Improve Order and Inventory Management for Your Business
Learn effective strategies to optimize order and inventory management for your business. Reduce errors, improve efficiency, and streamline operations.
Construction Material Storage: Reducing Waste and Improving Asset Tracking
Optimise construction material storage to cut waste and boost asset tracking. Improve material handling in construction for efficiency and cost savings.