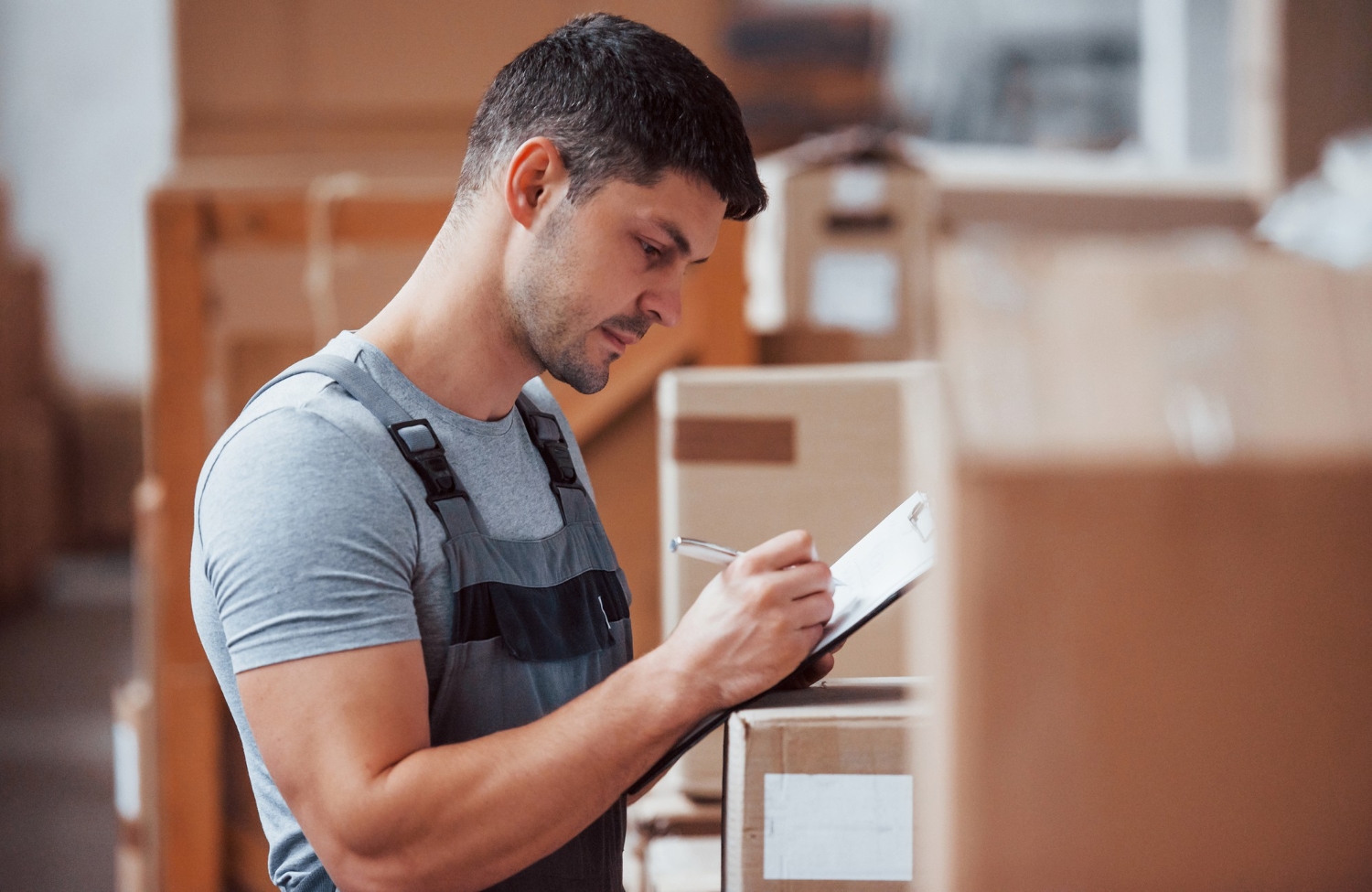
How To Calculate Beginning Inventory
Learning to negotiate the realm of inventory control can feel like trying to solve a difficult problem. The key to this riddle is beginning inventory, a basic idea that affects pricing policies and financial reporting, among other areas. Whether you know nothing about inventory monitoring or are an experienced business owner, knowing how to precisely calculate beginning inventory lays the groundwork for compliance with financial procedures and wise business decisions.
This all-inclusive guide examines its importance in corporate operations, breaks out the fundamentals of beginning inventory, and provides doable strategies for mastering its computation. By the conclusion, you will know and have the means to boldly monitor and evaluate this important business indicator, therefore optimising your inventory control for higher operational effectiveness and profitability.
What is Beginning Inventory?
Beginning inventory is the financial worth of every item, material, and thing a company owns at the start of a given accounting cycle. This vital inventory statistic shows the same precise value as the ending inventory from the previous accounting cycle, so establishing a consistent financial story across reporting years.
Unlike inventory purchased during the current period (new stock acquired), beginning inventory specifically captures what remained unsold from the previous period. This distinction matters significantly when calculating profitability metrics and understanding inventory flow.
The value of your beginning inventory directly influences several vital financial components:
- It serves as the foundation for calculating the Cost of Goods Sold (COGS), where beginning inventory + purchases – ending inventory = COGS
- It affects your balance sheet by representing a portion of your company’s assets
- It influences gross profit calculations, ultimately impacting your business’s reported profitability
Understanding the relationship between beginning inventory, ending inventory, and inventory purchased provides a complete picture of inventory movement throughout an accounting period—essential knowledge for business owners and financial analysts alike.
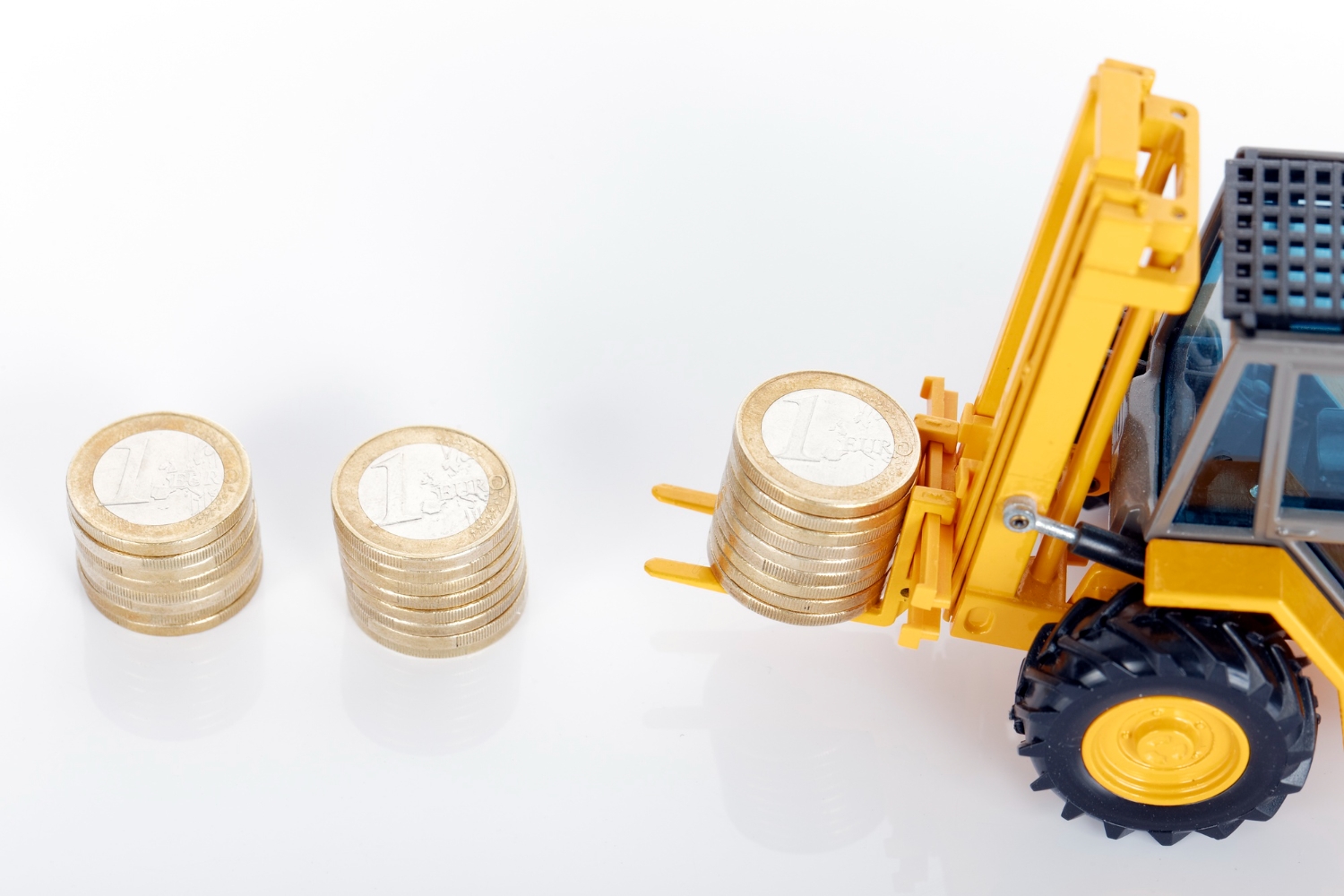
Why is Beginning Inventory Important?
Accurate beginning inventory figures serve as cornerstones of reliable financial reporting. When tax season arrives, these values directly impact your tax liability calculations and compliance requirements. Miscalculated inventory values can trigger audits or result in overpaid taxes—neither scenario is beneficial to your business.
Beyond reporting obligations, beginning inventory significantly shapes pricing strategies. With precise inventory valuations, businesses can:
- Determine true cost bases for products
- Set competitive yet profitable price points
- Track inventory holding costs accurately
The intricate connection between COGS, beginning inventory, and ending inventory reveals your operation’s efficiency. This relationship helps identify:
- Inventory turnover rates
- Product performance metrics
- Potential stockout or overstock situations
When beginning inventory increases without corresponding sales growth, it signals potential inventory management issues requiring immediate attention. On the other hand, steadily dropping beginning inventory levels could point to either better turnover or supply chain weaknesses.
Using beginning inventory data, smart companies project future inventory demands, therefore avoiding both expensive stockouts and too high holding costs. This proactive strategy turns a static asset into a strategic advantage.
How to Find Beginning Inventory
The standard beginning inventory formula employs a reverse calculation approach when direct counts aren’t available:
Beginning Inventory = Ending Inventory + Cost of Goods Sold – Purchases
This formula reflects the logical flow of inventory through your business operations. To implement this calculation successfully, each component requires careful consideration:
- Ending Inventory: Determined through physical counting, perpetual tracking systems, or estimation methods like retail or gross profit methods
- Cost of Goods Sold (COGS): Calculated from sales records multiplied by per-unit costs, requiring accurate cost assignment methods (FIFO, LIFO, or weighted average)
- Purchases: Documented through supplier invoices, purchase orders, and receiving reports, including all acquisition costs like freight and duties
The method you use to find beginning inventory often correlates with whether your business employs a periodic or perpetual inventory system. The difference between periodic and perpetual inventory systems becomes particularly evident here—periodic systems require manual calculations using the formula above. In contrast, perpetual systems can provide beginning inventory figures automatically through continuous tracking.
Accurate data collection forms the bedrock of reliable beginning inventory calculations. Modern online inventory management solutions streamline this process by automatically recording transactions and maintaining perpetual inventory records, reducing the complexity of finding accurate beginning inventory values.
Implementing structured procedures for documenting inventory movements becomes essential for businesses without sophisticated tracking systems. These procedures include standardised receiving protocols, regular cycle counts, and consistent expense categorisation.
Understanding how to properly apply the beginning inventory formula enables businesses to maintain accurate financial records even when traditional inventory counting proves challenging.
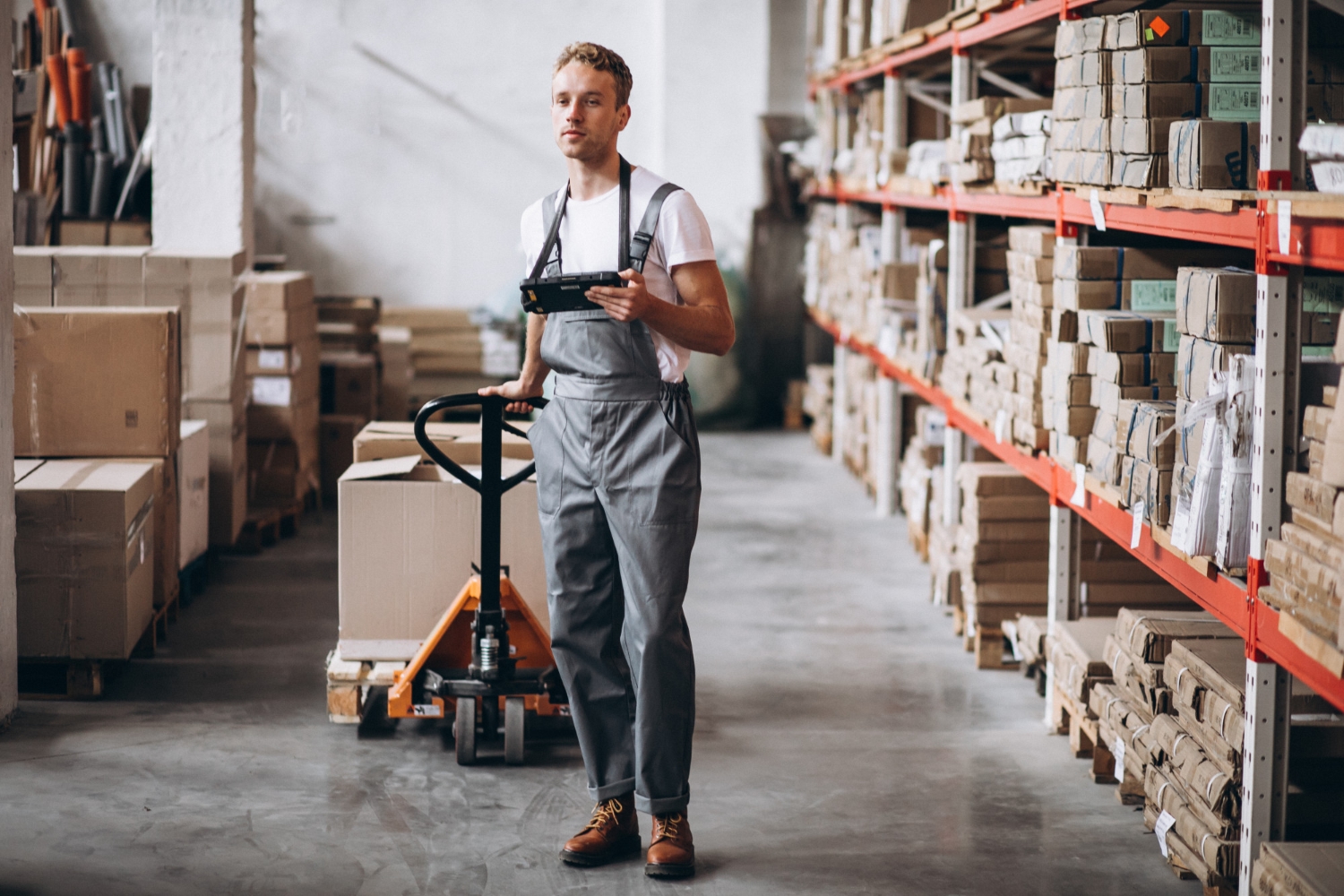
Step-by-Step Guide: How to Calculate Beginning Inventory
Finding your beginning inventory can follow multiple approaches depending on your available information. Here’s a comprehensive guide to calculating beginning inventory regardless of your starting point:
Method 1: Using the Previous Period's Ending Inventory
- Locate your previous accounting period’s final inventory count (physical or system-generated)
- Verify this figure against your accounting records to ensure accuracy
- This ending value becomes your new period’s beginning inventory
- Gather your current period’s ending inventory value
- Calculate your COGS for the period using sales and cost data
- Compile all inventory purchases made during the period
- Apply the formula: Beginning Inventory = Ending Inventory + COGS – Purchases
Method 3: Physical Counting Approach
- Schedule inventory counting immediately before the new accounting period
- Document quantities of all inventory items
- Apply appropriate valuation methods (FIFO, LIFO, weighted average)
- Calculate total inventory value based on quantities and unit costs
Method 4: When Opening a New Business
For new ventures without previous inventory history:
- Record all initial inventory purchases before opening
- This initial stock value becomes your first beginning inventory or opening inventory
- Document this figure as your starting point for future calculations
Each method has specific applications depending on your business circumstances, available data, and accounting practices. The goal remains consistent: establishing an accurate foundation for your period’s inventory calculations.
Common Mistakes When Calculating Beginning Inventory
Even experienced businesses encounter pitfalls when managing inventory valuations. Awareness of these common errors helps prevent costly mistakes:
Incomplete Purchase Tracking
Failing to capture all inventory-related costs—such as freight, duties, or returns—skews your beginning inventory calculations. This partial tracking creates cascading errors throughout your financial statements, affecting profitability metrics and tax calculations.
Timing Misalignments
Recording purchases or sales in mismatched accounting periods throws off the link between COGS, beginning inventory, and ending inventory. Businesses with large month-end transactions or suppliers from abroad especially suffer from this imbalance.
Confusion Between Similar Terms
Misinterpreting beginning inventory versus opening inventory introduces conceptual errors in financial analysis. While often used interchangeably, some accounting contexts distinguish between them based on business lifecycle or reporting requirements—a nuance requiring careful attention.
Inconsistent Counting Methodologies
Switching between different inventory valuation methods (FIFO, LIFO, weighted average) without proper adjustments creates incomparable beginning inventory figures across periods. This inconsistency undermines trend analysis and financial reporting integrity.
Overlooking Inventory Adjustments
Ignoring spoilage, damage, theft, or obsolescence results in too high beginning inventory values. Frequent inventory reconciliation finds these variances before they become major financial distortions.
Beyond simple paperwork annoyances, these mistakes profoundly skew your company’s financial picture, influencing stakeholder confidence, funding prospects, and strategic decision-making power.
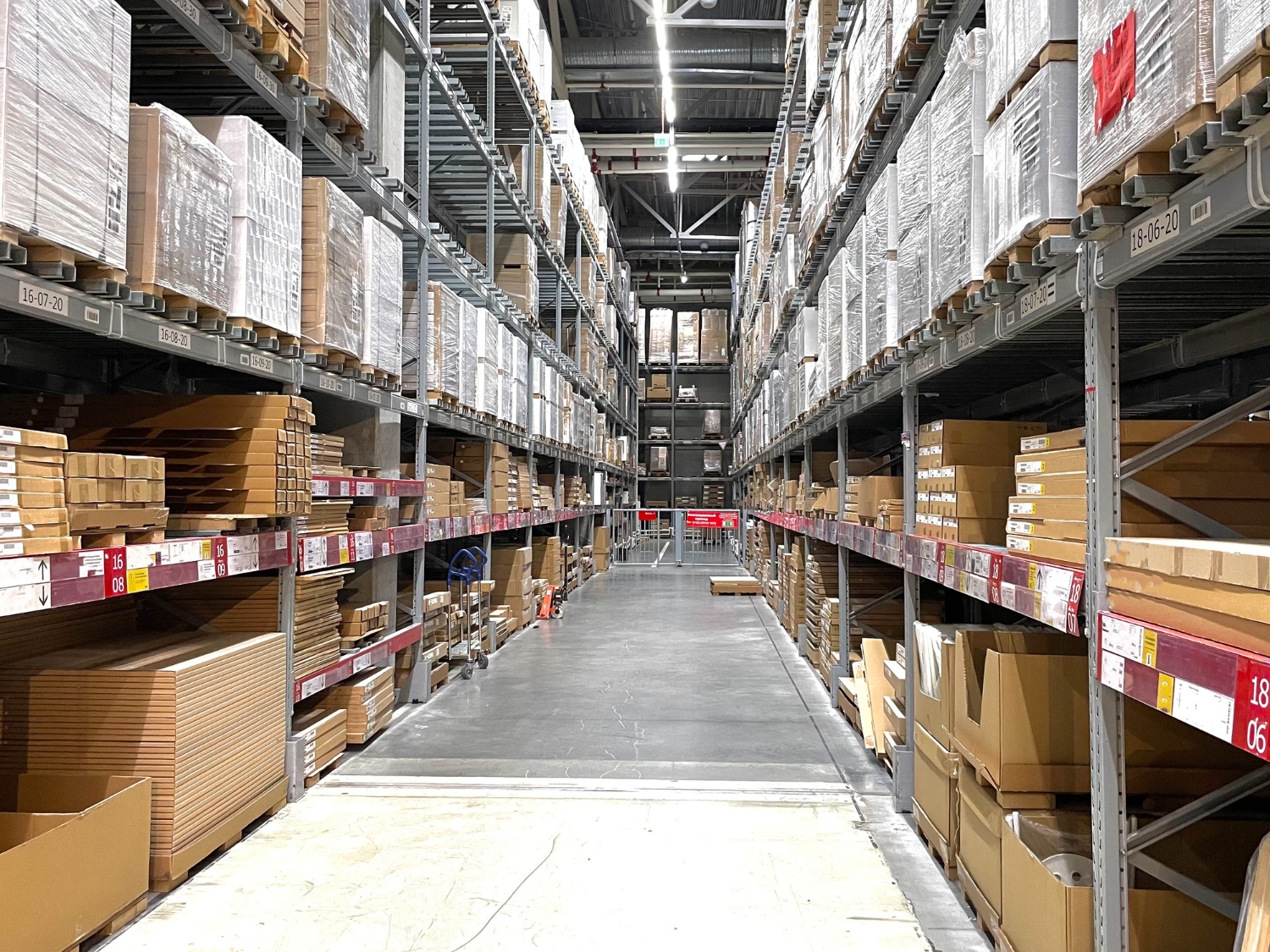
Tools and Software for Inventory Management
Modern inventory challenges demand sophisticated solutions. Contemporary businesses benefit from specialised tools that transform beginning inventory calculations from error-prone manual processes into streamlined, accurate operations.
Comprehensive Accounting Platforms
Systems like QuickBooks, Xero, and Sage provide integrated modules that automatically:
- Transfer ending inventory values to beginning inventory for new periods
- Calculate COGS based on recorded sales and inventory movements
- Generate reports showing the relationship between beginning inventory, ending inventory, and inventory purchased
Dedicated Inventory Management Systems
Purpose-built solutions offer enhanced inventory visibility:
- Barcode and RFID scanning capabilities for accurate physical counts
- Perpetual inventory tracking, eliminating manual calculation needs
- Automated reorder points prevent stockouts while optimising carrying costs
Asset Tracking Solutions
Comprehensive asset tracking systems extend beyond basic inventory counting to provide:
- Lifecycle management for valuable inventory assets
- Location tracking for distributed inventory
- Maintenance scheduling and depreciation calculations
- Integration with beginning inventory and ending inventory valuations
Small Business Solutions
Budget-conscious operations can leverage accessible options:
- Cloud-based inventory apps with basic tracking features
- Spreadsheet templates with built-in beginning inventory formula calculations
- Hybrid systems combining manual counts with digital record-keeping
Enterprise Resource Planning (ERP) Systems
Larger organisations benefit from comprehensive platforms:
- Multi-location inventory synchronisation
- Complex valuation method support (FIFO, LIFO, weighted average)
- Forecast modelling using historical beginning inventory trends
The automation of beginning and ending inventory calculations delivers benefits beyond time savings. It significantly reduces human error, improves data consistency, and provides real-time inventory visibility, which is crucial for agile business operations.
Key Takeaways: Mastering Beginning Inventory
Understanding and properly calculating beginning inventory stands as a fundamental skill for financial accuracy and business success. As we’ve explored throughout this guide, beginning inventory represents more than a static number—it forms a critical link in your financial reporting chain and inventory management strategy.
What is beginning inventory? It’s the monetary value of goods available at the start of an accounting period directly tied to the previous period’s ending inventory. This figure serves as the foundation for accurate COGS calculations and financial reporting.
When direct information is lacking, the beginning inventory formula offers a consistent approach for figuring inventory values. Businesses can learn a great deal about their operational effectiveness by knowing the links among beginning, ending, and purchased inventory.
Accurate beginning inventory calculations depend on consistent approaches, thorough record-keeping, and attention to inventory fluctuations over accounting periods. While challenges exist, modern tools significantly simplify these processes.
Itemit’s tracking system offers particularly robust solutions for businesses struggling with inventory management. Its comprehensive platform provides:
- Real-time inventory tracking across multiple locations
- Automated beginning inventory and ending inventory transfers between periods
- Customisable reporting showing the relationship between inventory values and profitability
- Cloud-based accessibility ensures consistent record-keeping regardless of physical location
- Scalable solutions growing alongside your business needs
Whether you calculate your beginning inventory manually or leverage sophisticated software solutions, the principles remain consistent: Accurate inventory valuation forms the foundation of sound financial management and business success.
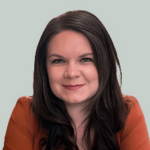
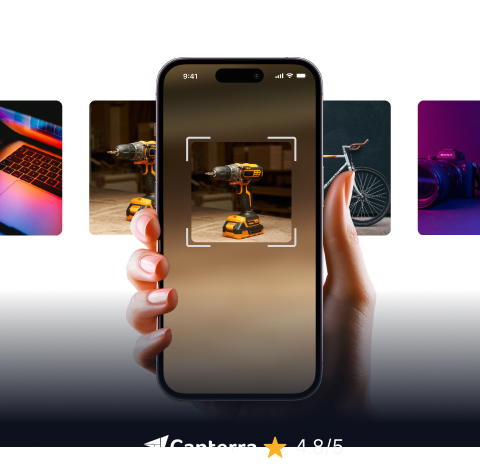
Try itemit
Choose a better way to track
your assets.
Start your free 14-day trial now!
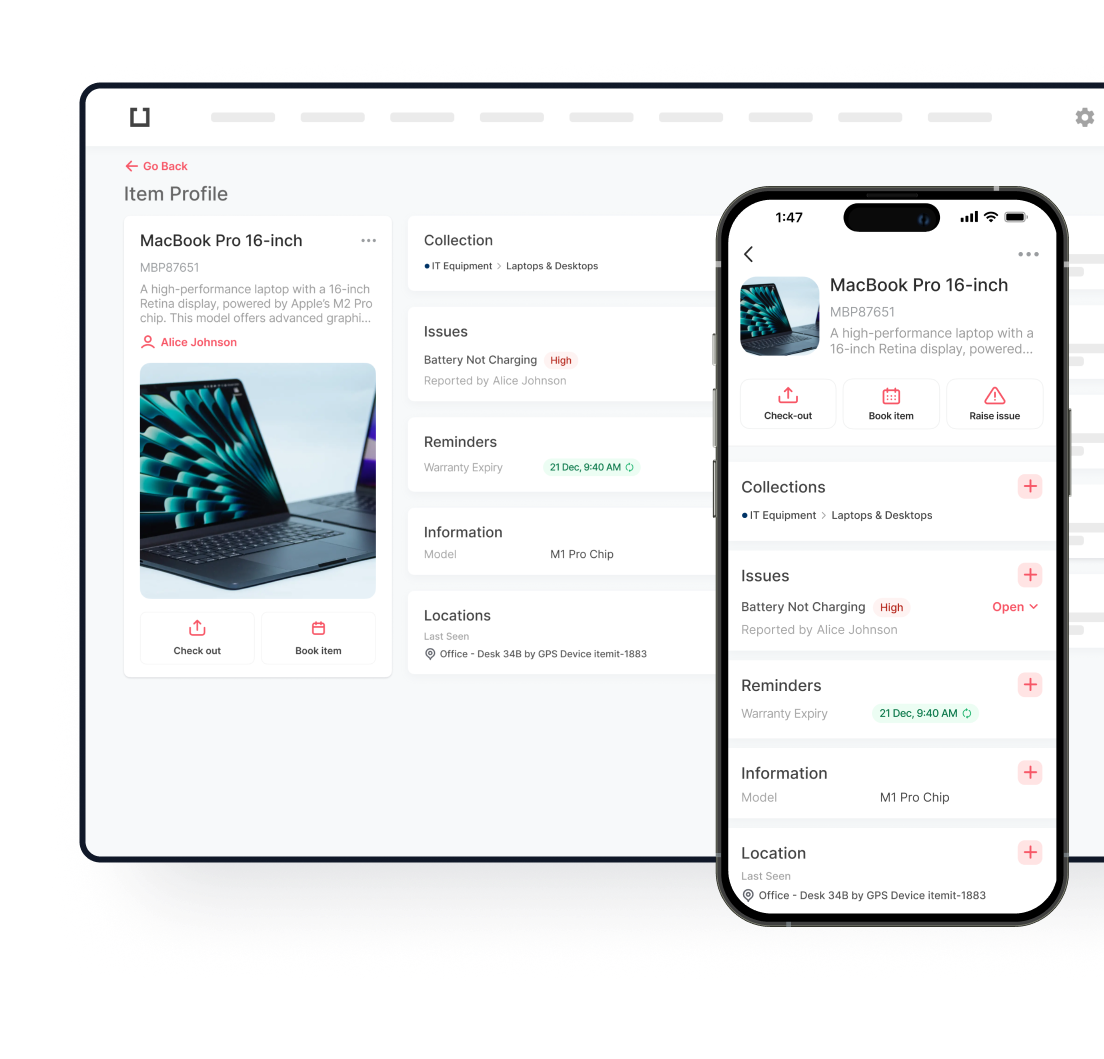
Keep Learning
itemit Blog
Tips, guides, industry best practices, and news.
How to Manage an Inventory Shortage and Prevent Stockouts
Struggling with stockouts? Discover how to manage inventory shortages, prevent disruptions, and optimize your supply chain with expert inventory management tips.
How to Improve Order and Inventory Management for Your Business
Learn effective strategies to optimize order and inventory management for your business. Reduce errors, improve efficiency, and streamline operations.
Exploring Different Types of Inventory and Their Impact on Asset Tracking
Learn about the 4 types of inventory—raw materials, WIP, finished goods, and MRO—and their impact on asset tracking. Discover strategies for better inventory management.