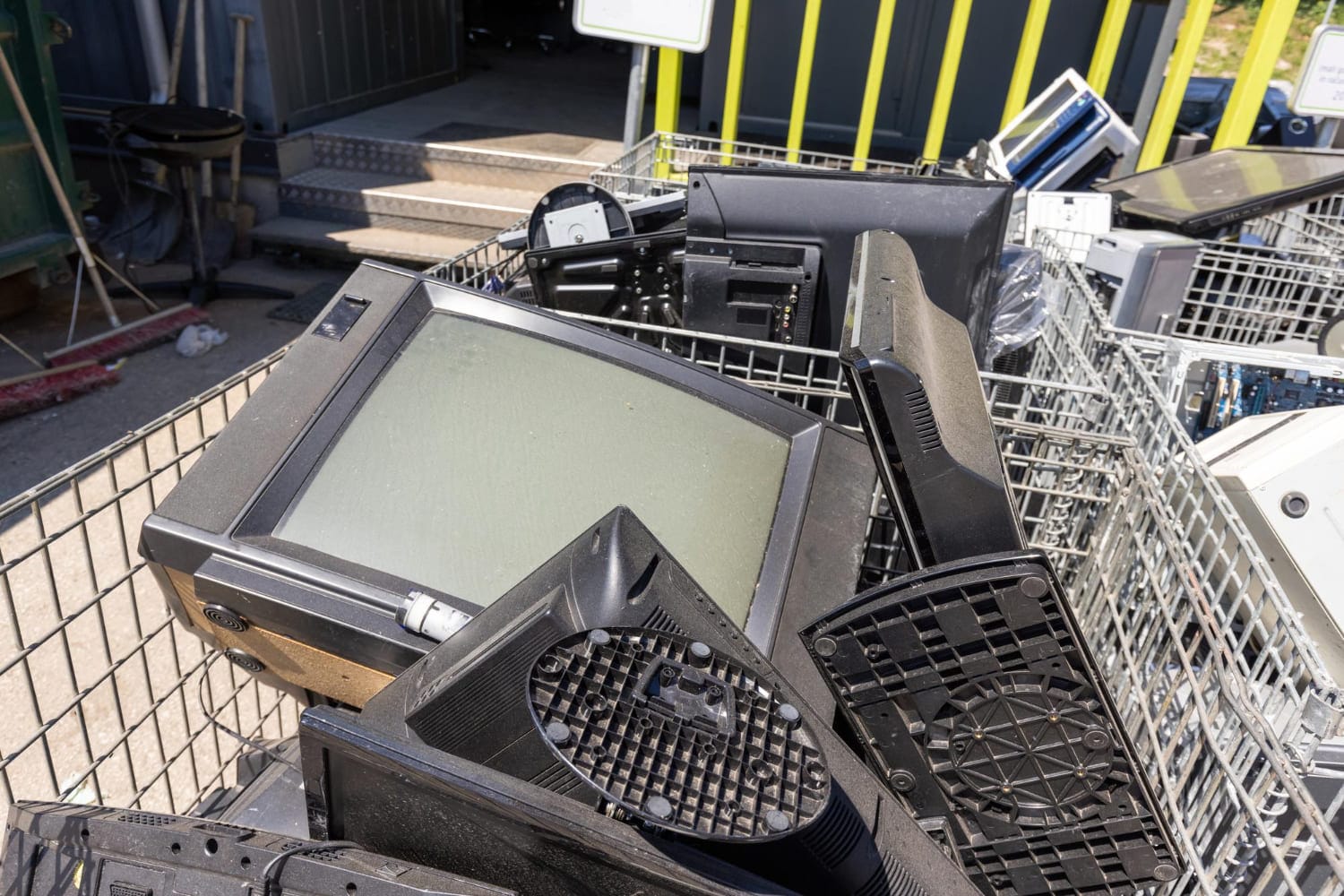
Not a lot of people are aware that there are four phases of the equipment life cycle. Perhaps many people assume that equipment is purchased, used, and discarded. However, the fact of the matter is that there’s much more to equipment use than this.
Understanding the four phases can help with equipment tracking. It can also give you a further understanding of what all types of equipment, such as tools, machinery, and computers go through. As a result, you may be more inclined to take better care of them so each tool or machine, etc., has a longer life. When equipment lasts longer, it can potentially be more productive and thereby increase the bottom line. This is where equipment life cycle management comes into play, ensuring that each phase is carefully monitored and optimised.
Planning
The first phase is planning, where careful consideration is given to the type of equipment needed and its intended purpose. This phase includes:
- Identifying what you need
- Determining the equipment’s purpose
- Assessing whether the equipment will improve operations
- Ensuring the budget allows for it
- Estimating depreciation and overall costs
Will the equipment you’re about to purchase fit your business’s needs? Will it contribute to operations and help to boost profits? These are things to consider before you purchase anything. Proper planning within equipment life cycle management helps ensure that the investment is sound and aligned with your business goals.
A well-planned strategy not only saves costs but also ensures that the equipment will be an asset, not a liability. Planning is crucial, as it lays the foundation for all subsequent phases and allows your business to avoid common pitfalls related to overspending or buying inadequate equipment.
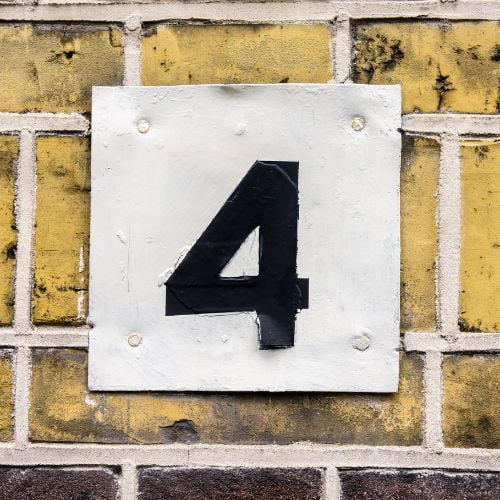
Acquisition
Once planning is complete, the next phase is acquisition. The acquisition or purchase of equipment is one of the most important but also one of the hardest parts of IT life cycle management. The right acquisition ensures that your equipment serves its intended purpose effectively and efficiently. If you fail to make the right purchase, production and profits could be negatively affected. Therefore, you need to:
- Work with your budget in mind, ensuring you purchase equipment suited to your business
- Identify the asset or service you wish to purchase
- Write up a shortlist of who you could purchase it from
- Try to negotiate a price and delivery, if necessary
- Agree and finalise the purchase(s)
The acquisition process is not just about buying the equipment; it also includes setting up systems to track it. Once you have purchased the right product, it’s important to add it to your asset tracking system. Doing so will allow you to monitor your new purchase throughout its life cycle. Many businesses also utilise an asset tracking app to streamline monitoring and ensure all equipment data is readily accessible. This step is crucial in ensuring that your asset begins its journey in your organisation with proper documentation and monitoring.
Operation and Maintenance

Once the equipment is acquired, we move into the operation and maintenance phase. This is ideally the longest phase in the life cycle and focuses on maximising the asset’s value. Proper maintenance can make all the difference in extending the useful life of your equipment.
The goals during this phase are:
- Improve operations and boost profits
- Ensure that the equipment reacts positively to upgrades, licenses, and repairs when necessary
- Regularly monitor the equipment and check for issues to prevent downtime
The operation part of phase three could potentially work out to be better than expected if a good maintenance plan is used. Lifecycle asset management during this phase focuses on maximising the productivity and longevity of each asset.
A maintenance plan can be useful when it is used alongside trusted equipment tracking software. Software such as this can help to:
- Reduce equipment downtime
- Lower the cost of emergency repairs
- Increase uptime
- Increase the asset’s life expectancy
By establishing a robust operation and maintenance plan, you can prevent unexpected issues and downtime. Proactive care during this stage is vital for maximising the return on investment. As we have already mentioned, it is hoped that this phase of the life cycle is the longest. However, when a piece of machinery is under constant use, it can suffer. Parts may fail to work as well as they should, the machine may overheat, etc. However, if the machine is looked after, disruptions can be kept to a minimum. There’s always a chance that such equipment could last longer than expected, ultimately benefiting the business.
Renewal Or Disposal

Eventually, every asset will reach the renewal or disposal phase. Every asset will come to the end of its life cycle at some stage. This is perfectly normal and something that all managers have to deal with. Ideally, any equipment that your business uses will last a long time. It should have been manufactured to a high standard and then used as intended during its working life.
Additionally, the maintenance plan should have ideally helped to keep the equipment working for perhaps longer than it was anticipated. Using a good maintenance plan alongside equipment tracking software will make a difference to longevity. However, after some time, all equipment eventually fails. It’s at this stage that it will either need to be renewed, if possible, sold, or disposed of.
If the equipment can be recycled, there’s an opportunity for it to gain a new life, so the four phases begin once more. Proper disposal or renewal is a significant part of life cycle replacement, ensuring that old assets are properly replaced in a timely manner.
If the equipment does need to be disposed of, it’s of prime importance that it is disposed of in an environmentally friendly manner. It is also important that any data should be wiped for security reasons. As soon as the equipment has been disposed of, it is time for a replacement to be used, and the four phases of the equipment life cycle begin once more.
The Importance of Equipment Life Cycle Management
With a better understanding of the four phases of an asset life cycle, one can realise how this is translated into very real business benefits. Properly managing equipment, computers, tools, and vehicles extends their useful life or enhances general business productivity. It also saves money and keeps the bottom line healthier – the dream of every business.
Thankfully, that can be done when these four phases are managed correctly – or better yet, optimally – with the help of equipment tracking software and a strategic equipment life cycle management approach. Proper life cycle management is difficult to overemphasise; it’s the only way to ensure each phase brings maximum value to your organisation.
Equipment life cycle management is more than understanding the phases; it involves proactively taking steps in each stage to improve your equipment. Proper lifecycle asset management offers an unrivalled ability to increase asset utilisation, reduce unplanned downtime, and ensure that the equipment contributes at maximum value during its lifetime.
The concept of an asset management lifecycle can be defined as a strategic approach to organisations that allows them to make proper decisions at every stage, from acquisition to disposal. Proper management also helps minimise costs associated with emergency repairs, therefore improving cost-effectiveness.
Asset Life Cycle Stages and Business Strategy
Each of the asset life cycle stages has a direct impact on your business strategy and operational efficiency. During the planning phase, identifying the right equipment that aligns with your business needs is crucial for success. In the acquisition phase, careful budgeting and sourcing can prevent unnecessary expenses, ensuring the best value for your investments. During operation and maintenance, proactive care extends the useful life of equipment, keeping productivity levels high. Finally, during the renewal or disposal phase, businesses need to make strategic decisions regarding whether to replace, upgrade, or properly dispose of assets.
Effective equipment life cycle management not only increases the lifespan of your assets but also enhances efficiency across all operations. When each stage is optimised, your business benefits from reduced costs, improved productivity, and a smoother operation overall. This kind of proactive approach to equipment management also helps businesses remain competitive, as they can better allocate resources and optimise processes without the interruptions caused by poorly maintained equipment.
Wish to speak with an expert about equipment tracking and life cycle management? Contact us now at: team@itemit.com.
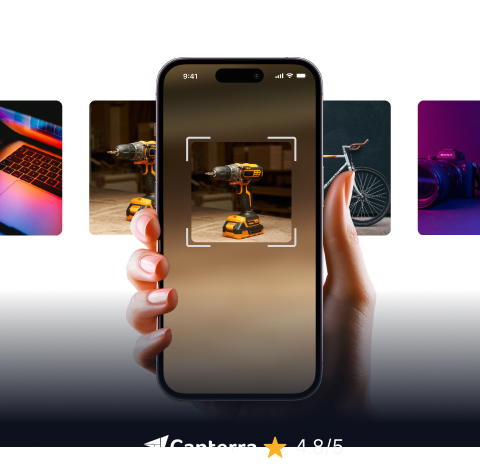
Try itemit
Choose a better way to track your assets. Start your free 14-day trial now!
Frequently Asked Questions
What is an asset life cycle, and why is it important?
The asset life cycle is the series of events an asset experiences, from planning and procurement to operation, maintenance, and disposal. Knowing the asset life cycle helps companies maximise the value of every asset, guaranteeing appropriate use, maintenance, and replacement when needed.
How does lifecycle asset management benefit equipment longevity?
In proactive maintenance, monitoring, and care during every phase of an asset’s life, lifetime asset management Businesses may greatly extend the useful lifetime of equipment and lower the need for early replacements by tracking maintenance plans and limiting downtime.
What are the stages of the equipment life cycle, and how do they impact planning?
The equipment life cycle consists of planning, purchase, operation and maintenance, and either disposal or renewal. Effective planning guarantees that the correct tools are bought, kept, and replaced at the appropriate moment, therefore ensuring better operational efficiency and cost savings at every level.
How does asset tracking help in managing the asset life cycle?
An asset tracking system or asset tracking software is indispensable in monitoring the asset life cycle. It records equipment locations, usage, and maintenance schedules in real time, helping guarantee timely maintenance, reduce the possibility of unplanned downtime, and prolong the lifetime of assets.
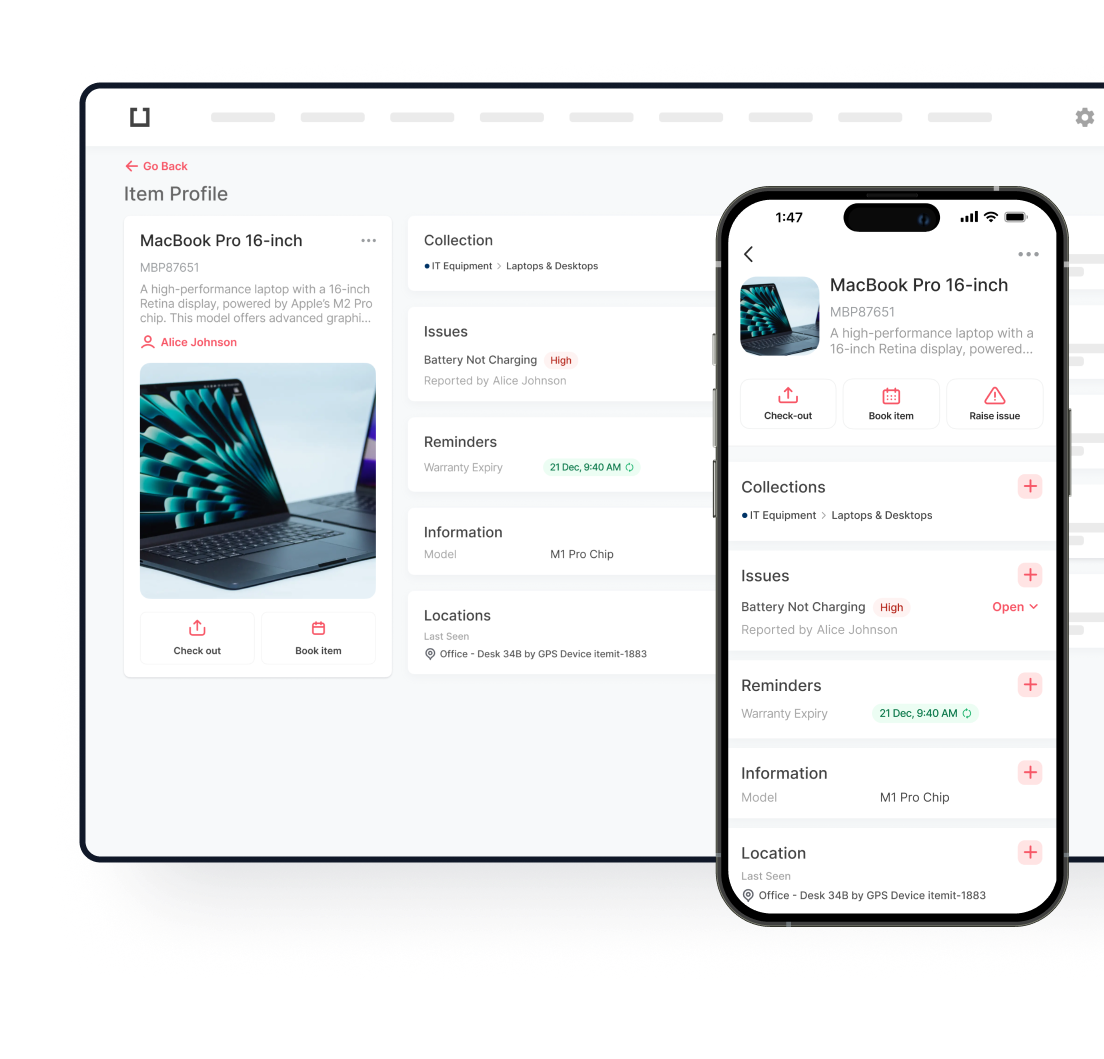
Keep Learning
itemit Blog
Tips, guides, industry best practices, and news.
What Is Visual Inspection? Definition, Methods, and Best Practices in Manufacturing
Learn the meaning of visual inspection, its methods, tools, and applications in manufacturing. Discover best practices for accurate quality control.
5 Tips For Better Equipment Management
Equipment management is vital to ensuring your business’s smooth operations. Discover how to get the most out of your hard-earned investments.
What is equipment booking software and do I need it?
What is equipment booking software? Should you use it if you’re hiring out or sharing equipment? How can itemit help you book equipment?